There are two things we’ve always believed at Hamilton By Design:
- Accuracy matters.
- If you can model it before you make it, do it.
That’s why when the FARO Focus S70 hit the scene in 2017, we were early to the party — not just because it was shiny and new (though it was), but because we knew it would change how we support our clients in mining, processing, and manufacturing environments.
The S70 didn’t just give us a tool — it gave us a superpower: the ability to see an entire site, down to the bolt heads and pipe supports, in full 3D before anyone picked up a wrench. Dust, heat, poor lighting — no problem. With its IP54 rating and extended temperature range, this scanner thrives where other tools tap out.
And we’ve been putting it to work ever since.
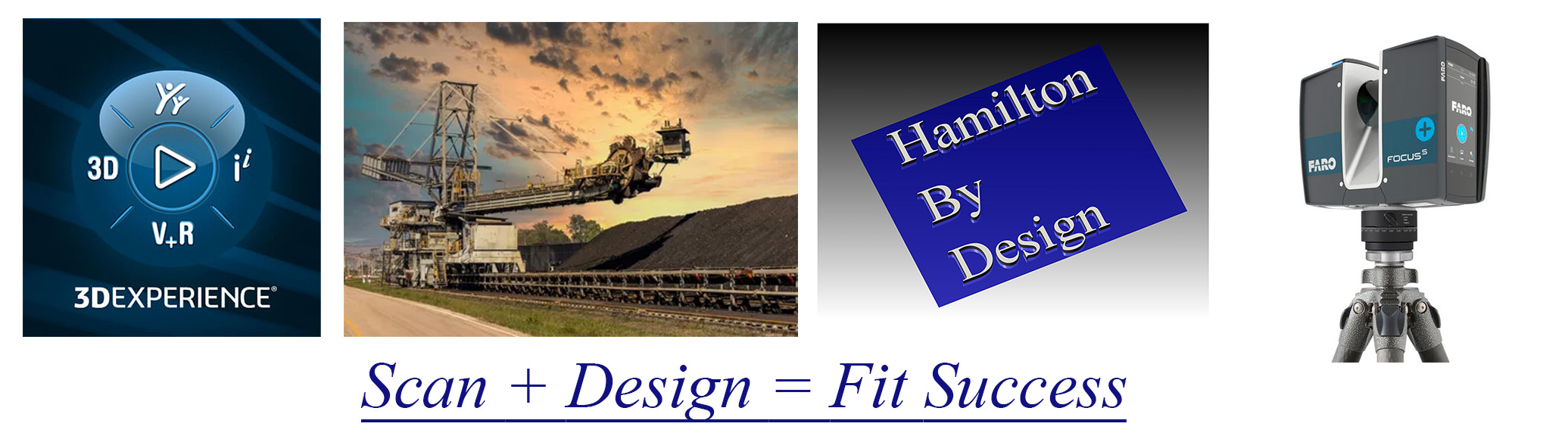
“Measure Twice, Cut Once” Just Got a Whole Lot More Real
Laser scanning means we no longer rely on outdated drawings, forgotten markups, or that sketch someone did on the back of a clipboard in 2004.
We’re capturing site geometry down to millimetres, mapping full plant rooms, structural steel, conveyors, tanks, ducts — you name it. And the moment we leave site, we’ve already got the data we need, registered and ready to drop into SolidWorks.
Which, by the way, we’ve been using since 2001.
Yes — long before CAD was cool, we were deep into SolidWorks building models, simulating loads, tweaking fit-ups, and designing smarter mechanical solutions for complex environments. It’s the other half of the story — scan it, then model it, all in-house, all under one roof.
Safety by Design – Literally
Here’s the part people often overlook: 3D laser scanning isn’t just about accuracy — it’s about safety.
We’ve worked across enough plants and mine sites to know that the real hazards are often the things you don’t see in a drawing. Tight access ways. Awkward pipe routing. Obstructions waiting to drop something nasty when a shutdown rolls around.
By scanning and reviewing environments virtually, we can spot those risks early — hazard identification before boots are even on the ground. We help clients:
- Reduce time-on-site
- Limit the number of field visits
- Minimise exposure to high-risk zones
- Plan safer shutdowns and installations
That’s a big win in any plant or processing facility — not just for compliance, but for peace of mind.
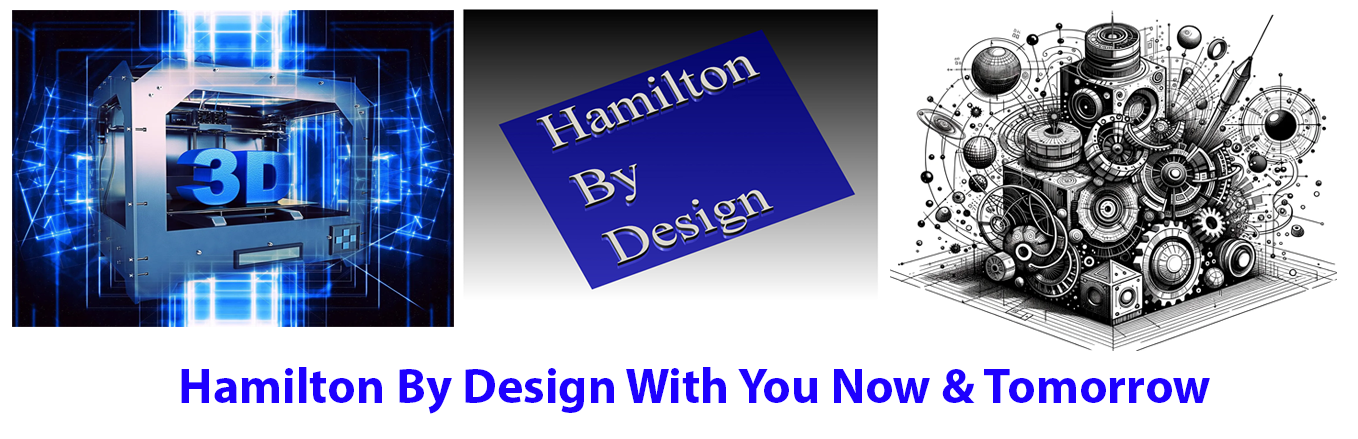
From Point Cloud to Problem Solved
Since 2017, our scanning and modelling workflows have supported:
- Brownfield upgrade projects
- Reverse engineering of legacy components
- Fabrication and installation validation
- Creation of digital twins
- Asset audits and documentation updates
And when you pair that with 24 years of SolidWorks expertise, you get more than just a pretty point cloud — you get practical, buildable, fit-for-purpose engineering solutions backed by deep industry knowledge.
Thinking about your next project? Let’s make it smarter from the start.
We’ll scan it, model it, and engineer it as we have been doing for decades — with zero guesswork and full confidence.
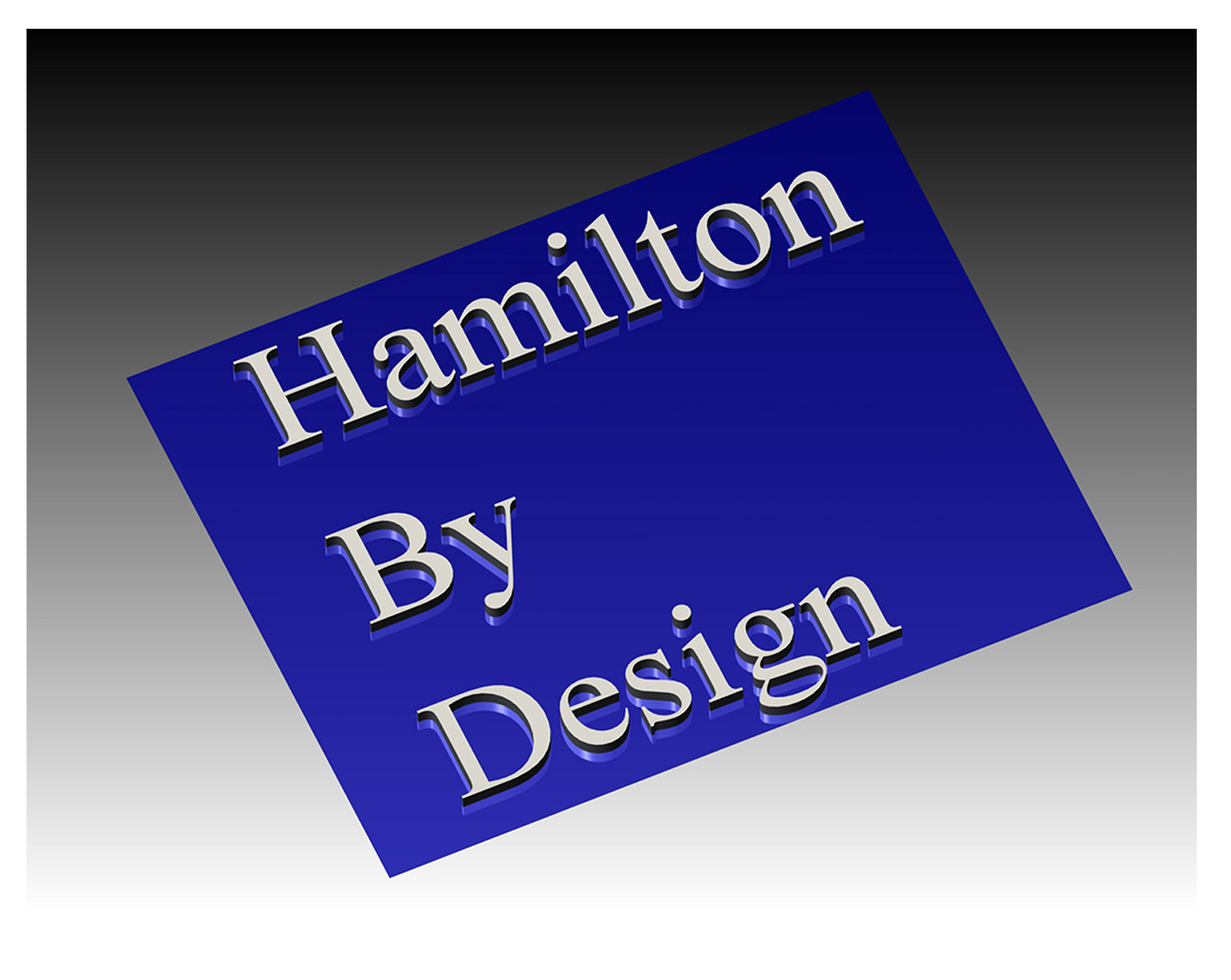
Mechanical Engineering | Structural Engineering
Mechanical Drafting | Structural Drafting
3D CAD Modelling | 3D Scanning
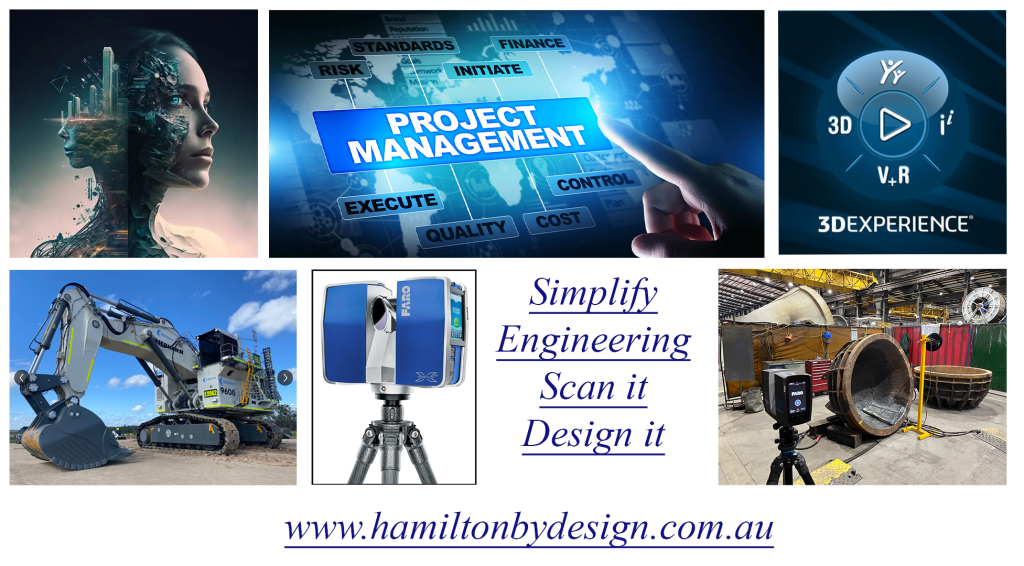
3D Cad Design | 3D Modelling | 3D Laser Scanning | Local Scanning
3D Scanning Brisbane | 3D Scanning Perth | 3D Scanning Melbourne
Laser scanning Central Coast
Laser Scanning for Engineering
SolidWorks | SolidWorks CAD Design | SolidWorks Mechanical Design
SolidWorks Structural Design | SolidWorks Smart Structures