Introduction
The smelting industry in Australia is a cornerstone of the nation’s economy, playing a crucial role in the production of essential metals such as aluminum, copper, and zinc. However, this sector faces significant challenges, ranging from stringent environmental regulations and high energy costs to supply chain disruptions and workforce shortages. Mechanical engineering consultants can offer invaluable assistance to smelting companies in navigating these challenges through their expertise in technology, process optimization, and regulatory compliance. This essay explores the biggest issues facing smelting companies in Australia today and how mechanical engineering consultants can help mitigate these challenges.
Environmental Regulations and Sustainability
Stringent Emissions Standards
One of the most pressing issues for smelting companies is complying with stringent emissions standards. The smelting process generates substantial greenhouse gases (GHGs) and other pollutants, leading to increased regulatory scrutiny. Mechanical engineering consultants can assist by designing and implementing advanced emissions control systems. These systems, such as scrubbers, filters, and catalytic converters, can significantly reduce the release of harmful pollutants.
Consultants like Hamilton By Design can also perform emissions audits to identify areas where improvements are needed and develop strategies to meet or exceed regulatory requirements. By integrating best practices in environmental engineering, consultants help smelting companies achieve compliance while minimizing operational disruptions.
Waste Management
Effective waste management is another critical challenge. The smelting process produces by-products like slag and other residues, which must be managed properly to avoid environmental harm. Mechanical engineering consultants can develop waste treatment and recycling processes that reduce waste volumes and promote the reuse of materials.
For example, consultants can design systems to process slag into valuable by-products such as construction materials. This not only helps in waste reduction but also provides an additional revenue stream for smelting companies. Moreover, consultants can help implement closed-loop systems that recycle water and other resources, further enhancing sustainability.
Energy Costs and Supply
High Energy Consumption
Smelting is an energy-intensive industry, and high energy costs can significantly impact profitability. Mechanical engineering consultants can conduct energy audits to identify inefficiencies and recommend improvements. By optimizing furnace operations, enhancing heat recovery systems, and upgrading to more energy-efficient equipment, consultants can help reduce energy consumption.
Additionally, consultants can assist in integrating renewable energy sources, such as solar or wind power, into smelting operations. This transition not only helps in reducing energy costs but also aligns with global sustainability goals. Consultants can design hybrid systems that ensure a reliable energy supply while maximizing the use of renewable sources.
Renewable Energy Integration
Transitioning to renewable energy is complex, requiring significant modifications to existing infrastructure. Mechanical engineering consultants can design and implement energy storage solutions, such as batteries or thermal storage systems, to address the intermittent nature of renewable energy sources. They can also develop grid management strategies that balance energy supply and demand, ensuring stable operations.
Consultants can evaluate the feasibility of various renewable energy projects, perform cost-benefit analyses, and assist in securing funding or incentives for these initiatives. By providing comprehensive planning and implementation support, mechanical engineering consultants enable smelting companies to successfully integrate renewable energy and reduce their carbon footprint.
Raw Material Availability and Costs
Supply Chain Disruptions
The availability and cost of raw materials are crucial factors for the smelting industry. Supply chain disruptions, caused by geopolitical tensions, natural disasters, or logistical challenges, can severely impact operations. Mechanical engineering consultants can help smelting companies build more resilient supply chains by optimizing procurement processes and developing strategic sourcing plans.
Consultants can also assist in identifying alternative raw material sources and establishing long-term contracts to ensure a stable supply. By analyzing market trends and performing risk assessments, consultants help companies anticipate potential disruptions and develop contingency plans.
Global Market Dynamics
Fluctuations in global demand and supply significantly affect raw material prices. Mechanical engineering consultants can provide market intelligence and predictive analytics to help smelting companies navigate these uncertainties. By leveraging data-driven insights, companies can make informed decisions on raw material purchases, inventory management, and production planning.
Consultants can also design flexible manufacturing systems that can quickly adapt to changes in raw material availability or cost. These systems can include modular equipment and scalable processes that allow for rapid adjustments to production volumes, helping companies remain competitive in a volatile market.
Technological Advancements
Modernization Needs
Many smelting facilities operate with aging infrastructure that is less efficient and more costly to maintain. Mechanical engineering consultants can design and implement modernization projects to upgrade equipment and improve operational efficiency. This includes adopting new technologies such as automation, robotics, and advanced control systems.
For example, consultants can develop automated systems for material handling and processing, reducing labor costs and increasing productivity. They can also implement advanced monitoring and control systems that optimize furnace operations, improve energy efficiency, and reduce emissions. By modernizing facilities, consultants help smelting companies enhance performance and competitiveness.
Innovation Investment
Continuous innovation is essential for the smelting industry to improve processes and develop new products. Mechanical engineering consultants can support research and development (R&D) efforts by providing technical expertise and project management skills. They can help design experiments, prototype new technologies, and scale up successful innovations for commercial use.
Consultants can also facilitate collaboration with academic institutions, industry consortia, and government agencies to leverage external knowledge and resources. By driving innovation, mechanical engineering consultants enable smelting companies to stay ahead of the competition and meet evolving market demands.
Workforce and Skills Shortages
Skilled Labor Deficit
The smelting industry faces a growing deficit of skilled labor, exacerbated by an aging workforce and insufficient training programs. Mechanical engineering consultants can help address this issue by developing comprehensive training and development programs. These programs can include on-the-job training, apprenticeships, and partnerships with educational institutions to build a pipeline of skilled workers.
Consultants can also design user-friendly systems and processes that reduce the reliance on highly specialized skills. For example, implementing automated systems with intuitive interfaces can simplify complex tasks, making them more accessible to less experienced workers. By enhancing workforce capabilities, consultants help smelting companies maintain productivity and operational efficiency.
Workforce Training
Continuous training is crucial to keep pace with technological advancements and regulatory changes. Mechanical engineering consultants can develop and deliver training programs that cover new technologies, safety protocols, and compliance requirements. These programs can be tailored to different levels of expertise, ensuring that all employees receive relevant and practical training.
Consultants can also implement training management systems that track employee progress, identify skill gaps, and schedule ongoing training sessions. By fostering a culture of continuous learning, consultants help smelting companies build a more adaptable and skilled workforce.
Economic and Market Pressures
Market Competition
The global smelting industry is highly competitive, with companies from countries with lower production costs posing significant challenges. Mechanical engineering consultants can help Australian smelting companies improve efficiency and reduce costs through process optimization and lean manufacturing principles. By streamlining operations and eliminating waste, companies can enhance productivity and profitability.
Consultants can also assist in developing new products and entering new markets, diversifying revenue streams and reducing dependence on traditional markets. By leveraging engineering expertise and market insights, consultants help companies navigate competitive pressures and achieve sustainable growth.
Economic Uncertainty
Economic downturns and fluctuations in demand for metals can significantly impact the smelting industry. Mechanical engineering consultants can help companies build resilience to economic uncertainty by developing flexible manufacturing systems and robust financial strategies. This includes scenario planning, stress testing, and the implementation of cost-control measures.
Consultants can also support diversification efforts by identifying new applications for smelted metals and exploring opportunities in emerging markets. By providing strategic guidance and technical solutions, consultants help smelting companies mitigate the impact of economic volatility.
Community and Social License to Operate
Community Relations
Maintaining positive relationships with local communities is essential for the smelting industry. Mechanical engineering consultants can help companies engage with communities through transparent communication and proactive initiatives. This includes designing and implementing environmental and social responsibility programs that address community concerns and contribute to local development.
For example, consultants can develop systems to monitor and reduce environmental impacts, such as air and water pollution, and provide regular updates to community stakeholders. They can also assist in developing community engagement plans that involve local residents in decision-making processes and ensure their voices are heard.
Indigenous Rights
Respecting Indigenous land rights is another critical issue for the smelting industry in Australia. Mechanical engineering consultants can support companies in engaging with Indigenous communities and ensuring their rights are respected. This involves conducting cultural heritage assessments, obtaining necessary permissions, and involving Indigenous representatives in project planning and implementation.
Consultants can also develop programs that support Indigenous employment and economic development, fostering positive relationships and building trust with Indigenous communities. By prioritizing social responsibility, consultants help smelting companies maintain their social license to operate.
Regulatory Compliance and Governance
Complex Regulatory Environment
Navigating the complex regulatory environment in Australia requires dedicated resources and expertise. Mechanical engineering consultants can help smelting companies establish robust compliance programs that ensure adherence to local, state, and federal regulations. This includes conducting regular audits, developing compliance protocols, and training employees on regulatory requirements.
Consultants can also assist in maintaining open lines of communication with regulatory bodies, ensuring that companies stay informed about regulatory changes and are prepared to respond proactively. By enhancing compliance and governance practices, consultants help companies avoid penalties and build trust with stakeholders.
Corporate Governance
High standards of corporate governance and transparency are essential for building trust with investors, customers, and communities. Mechanical engineering consultants can support companies in implementing best practices in governance, such as ensuring board diversity, developing risk management frameworks, and maintaining transparent reporting practices.
Consultants can also help companies align their operations with global standards, such as the United Nations Global Compact, demonstrating their commitment to ethical business practices and sustainability. By strengthening corporate governance, consultants help smelting companies enhance their reputation and attract investment.
Conclusion
The smelting industry in Australia faces a myriad of challenges, including stringent environmental regulations, high energy costs, supply chain disruptions, workforce shortages, and economic pressures. Mechanical engineering consultants play a crucial role in helping companies navigate these challenges by providing expertise in technology, process optimization, and regulatory compliance. By leveraging the skills and knowledge of mechanical engineering consultants, smelting companies can enhance efficiency, reduce costs, improve sustainability, and maintain competitiveness in a rapidly evolving
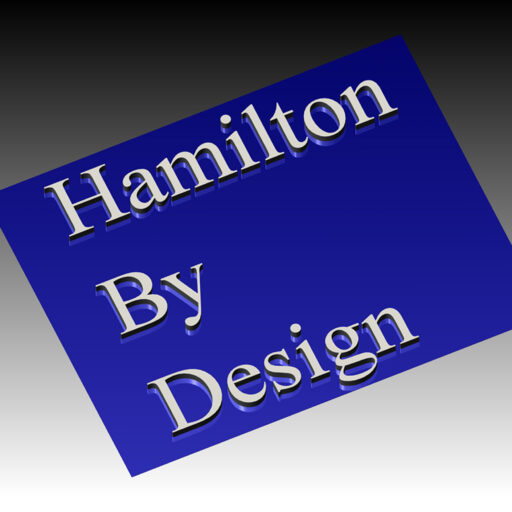
Mechanical Engineering | Structural Engineering
Mechanical Drafting | Structural Drafting
3D CAD Modelling | 3D Scanning
Hamilton By Design