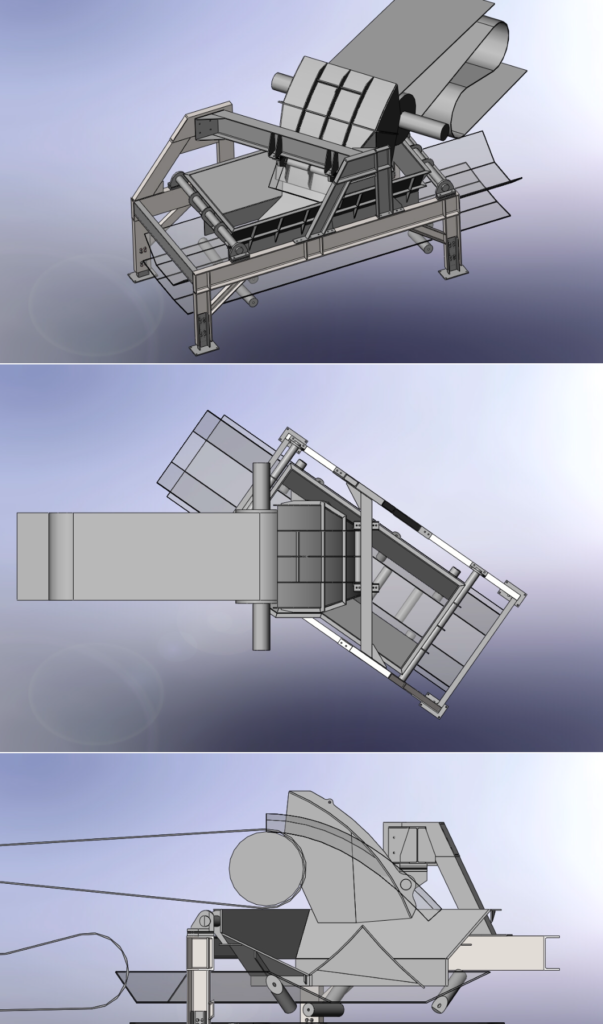
The challenges Mechanical Engineers have when it comes to maintaining the reliability of conveyor systems for transporting bulk materials, particularly particles ranging from 1mm to 100mm, presents mechanical engineers with a host of challenges. Reliability maintenance aims to ensure that these systems operate consistently and efficiently over their operational lifespan, minimizing downtime and optimizing productivity. Here are some key challenges faced by mechanical engineers in this regard:
1. Component Wear and Failure: The continuous operation of conveyor systems subjects various components such as belts, rollers, bearings, and drive mechanisms to wear and potential failure. The abrasive nature of bulk materials can accelerate this process, leading to shortened component lifespan and increased risk of unexpected breakdowns. Mechanical engineers must implement proactive maintenance strategies, including regular inspections, lubrication, and component replacement, to mitigate wear-related issues and enhance system reliability.
2. Material Contamination and Blockages: Bulk materials containing particles of diverse sizes can lead to material contamination and blockages within conveyor systems if not properly managed. Fine particles may accumulate in chutes, transfer points, or on conveyor surfaces, causing flow disruptions and increased friction. Engineers need to design systems with effective cleaning mechanisms, such as scrapers, brushes, and air blowers, to prevent material buildup and maintain uninterrupted material flow.
3. Misalignment and Tracking Issues: Misalignment of conveyor belts and tracking problems can result in uneven material distribution, increased friction, and premature wear on system components. Mechanical engineers must ensure proper belt tensioning and alignment during installation and implement monitoring systems to detect and correct any deviations from the desired trajectory. Advanced tracking technologies, such as automated belt positioners and laser alignment tools, can aid in maintaining optimal conveyor performance.
4. Environmental Factors: Harsh environmental conditions, including temperature variations, moisture, dust, and corrosive substances, pose significant challenges to conveyor system reliability. Exposure to such elements can accelerate component degradation and compromise system integrity. Engineers must select durable materials, coatings, and sealing solutions resistant to environmental hazards and implement preventive measures, such as regular cleaning and protective enclosures, to safeguard conveyor systems from adverse effects.
5. Safety and Regulatory Compliance: Compliance with safety regulations and industry standards is essential for ensuring the reliability and safe operation of conveyor systems. Mechanical engineers must stay abreast of regulatory requirements and design systems that meet or exceed applicable standards for material handling equipment. Regular safety inspections, training programs for personnel, and implementation of safety protocols are crucial aspects of reliability maintenance in conveyor systems.
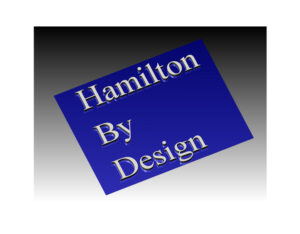
At Hamilton By Design, our team have the experience in addressing these challenges requires a comprehensive approach that combines sound engineering principles, advanced technologies, and proactive maintenance practices. By implementing robust reliability maintenance programs, mechanical engineers can maximize the uptime and longevity of conveyor systems for transporting bulk materials, thereby optimizing operational efficiency and minimizing costly disruptions.
Mechanical Engineering | Structural Engineering
Mechanical Drafting | Structural Drafting
3D CAD Modelling | 3D Scanning
Hamilton By Design